What are the design and processing processes of plastic injection molds?
2023-04-12
To make a good injection mold, there are many factors to consider, including design and processing procedures. Generally, the design and processing of injection molds require the following processes.
1、 Preparation work before design
1. Communicate with customers in detail and develop an injection mold design task book;
2. Familiar with the structure of plastic parts to be processed, including the geometric shape of plastic parts, the requirements for the use of injection molded parts, the surface and internal treatment requirements of injection molded parts, and the production materials of injection molded parts;
3. Check the molding process of plastic parts;
4. Clarify the model and specifications of the injection molding machine.
2、 Develop a molding process card
1. Clarify the basic information of the product, such as schematic diagram, weight, wall thickness, projected area, external dimensions, whether there are side indentations and inserts.
2. Overview of the raw materials used in the product, such as product name, model, manufacturer, color, and drying condition.
3. The main technical parameters of the selected injection molding machine, such as the relevant dimensions between the injection molding machine and the installation mold, screw type, power, etc.
4. Clarify the pressure and stroke of the injection molding machine.
5. Considering the injection molding conditions comprehensively, such as temperature, pressure, speed, locking force, etc.
3、 Structural design steps for injection molding molds
1. Determine the number of cavities. Conditions: maximum injection volume, locking force, product accuracy requirements, and economy.
2. Select the parting surface. The principle should be that the mold structure is simple, the parting is easy, and it does not affect the appearance and use of plastic parts.
3. Determine the layout plan of the cavity. Try to use a balanced arrangement as much as possible.
4. Determine the pouring system. Including main flow channel, diversion channel, gate, cold material hole, etc.
5. Determine the demolding method. Design different demolding methods based on the different parts of the plastic parts left in the mold.
6. Determine the structure of the temperature control system. The temperature control system is mainly determined by the type of plastic.
7. When determining the use of a block structure for the concave mold or core, the feasibility of machining and the installation and fixation method should be determined by dividing the block into blocks and simultaneously inserting them.
8. Determine the exhaust form. Generally, exhaust can be achieved by utilizing the gap between the mold parting surface and the ejection mechanism, while for large and high-speed injection molds, corresponding exhaust forms must be designed.
9. Determine the main dimensions of the injection mold. Calculate the working dimensions of the formed parts and determine the thickness of the side walls of the mold cavity, the bottom plate of the cavity, the core cushion plate, the thickness of the moving template, the thickness of the cavity plate of the modular cavity, and the closing height of the injection mold according to the corresponding formulas.
10. Choose a standard mold base. Select the standard mold base for injection molds based on the main dimensions of the designed and calculated injection molds, and try to select standard mold parts as much as possible.
11. Draw a structural sketch of the mold. Drawing a complete structural sketch of an injection mold is a crucial task in mold design.
12. Verify the dimensions of the mold and injection machine. Verify the parameters of the injection machine used, including maximum injection volume, injection pressure, locking force, and the dimensions of the installation part of the mold, mold opening stroke, and ejection mechanism.
13. Review of injection mold structure design. Conduct preliminary review and obtain the user's consent, while it is necessary to confirm and modify the user's requirements.
14. Draw the assembly diagram of the mold. Clearly state the assembly relationship, necessary dimensions, serial numbers, detailed lists, title blocks, and technical requirements of each part for injection molding (the content of the technical requirements includes the following: 1. performance requirements for the mold structure, such as assembly requirements for the ejection mechanism and core pulling mechanism; 2. requirements for the mold assembly process, such as the fitting gap of the parting surface and the parallelism between the upper and lower parts of the mold; 3. requirements for the use of the mold; 4. requirements for anti oxidation treatment, mold number, engraving, oil seal, and storage; 5. requirements for mold testing and inspection.).
15. Draw mold part drawings. The order of disassembling and drawing part drawings from mold assembly drawings or component drawings is: first inside then outside, first complex then simple, first formed parts then structural parts.
16. Review the design drawings. The final review of injection mold design is the final checkpoint of injection mold design, and more attention should be paid to the machining performance of the parts.
Cobtact Us
Add:No. 3, Bohai Road 015559, Yangzi Street, Binhai District, Weifang City, Shandong Province
Website
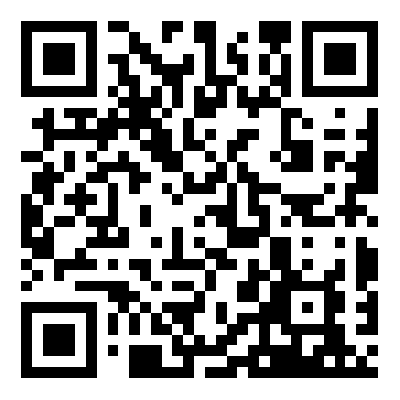